Keine Angst vor digitalen Innovationen
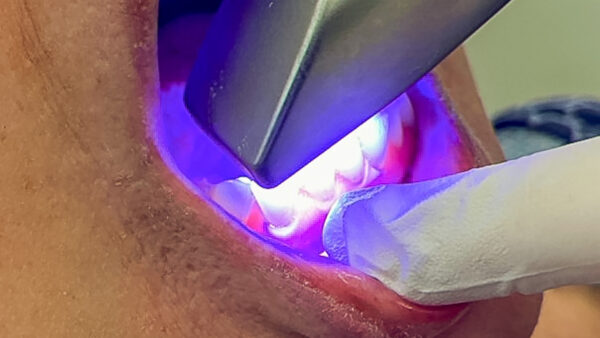
Digitale Lösungen bieten der Zahnheilkunde ein breites Feld an Prozessvereinfachungen und innovativen Arbeitsabläufen. Ein gutes Beispiel für die neuen Möglichkeiten ist die Herstellung von adjustierten Aufbissbehelfen für Patienten mit Bruxismus. Was früher viele und häufig aufwendige Arbeitsschritte erforderte, lässt sich heute dank digitaler Technik in saubereren und bequemeren Prozessen bewältigen. Die Erleichterungen sind spürbar, sowohl für die Patienten wie auch für das Team.
Eine entscheidende digitale Neuerung, mit der ich bereits seit vielen Jahren arbeite, ist sicherlich der Einsatz eines modernen Intraoralscanners, mit dessen Hilfe ich hochpräzise digitale Ganzkiefer-Abformungen vornehme. Und meinen Patienten wird durch diese Technologie die häufig als sehr unangenehm erlebte Gebissabformung erspart. Keine Materialrückstände in der Mundhöhle, kein Würgereiz, kein minutenlanges Ausharren mit der Gefahr des Misslingens einer ganzen Abformung. Diese Technik ermöglicht es mir, Aufbissbehelfe, Kronen, Brücken, Inlays und Implantat-Suprakonstruktionen zügig und komfortabel am Rechner in einer separaten Software zu konstruieren.
Mittlerweile möchte ich allerdings nicht nur Zahnersatz digital abformen und im Praxislabor produzieren können, sondern auch adjustierte Aufbissbehelfe. Bisher lief deren Produktion in meiner Praxis rein analog und wurde von meinen Praxismitarbeitern in aufwendiger Handarbeit bewältigt.
Investition 3D-Drucker
Die Anschaffung eines dentalen 3D-Druckers war also dafür der nächste erforderliche Schritt, der die MDR-konforme, zertifizierte Herstellung verschiedenster Behelfe ermöglicht: temporäre Kronen und Brücken, definitive Kronen, Prothesen, Löffel, Modelle, Bohrschablonen. Und eben auch Bissschienen.
Ich habe mich für den Drucker 3Demax von DMG entschieden. Überzeugt hat mich dabei der nahtlos zertifizierte Workflow bestehend aus Software, Hardware und Material: DMG bietet dafür präzise zusammenarbeitende Bausteine an, mit denen – auch bei verschiedensten Materialien – konstant und zuverlässig hochwertige Druckerzeugnisse gewährleistet sind. Die Dokumentation läuft, genau wie die Materialidentifizierung und Prozess-Steuerung, automatisch und vermeidet damit Fehldurchläufe und Programmunsicherheiten. Dass der 3D-Drucker außerdem besonders zügig arbeiten kann, gab meiner Entscheidung den letzten Schubs.
Der digitale Arbeitsprozess
Der nunmehr vollständig digitale Workflow besteht aus der digitalen Abformung am Patienten, der Konstruktion der Schiene am Rechner, dem eigentlichen Druckprozess, der Nachbearbeitung in der Reinigungs- und Nachbelichtungseinheiten sowie der Ausarbeitung und Politur mit Handstück.
Meine Mitarbeiterinnen scannen zunächst selbstständig den Ober- und Unterkiefer (Abb. 1).
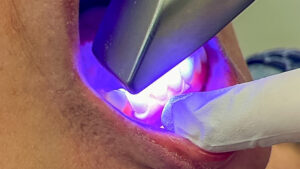
Abb. 1 – Scan von Ober- und Unterkiefer
Mit einem Kunststoff-Jig Regio 33–34 und 43–44 wird der Biss dafür um ca. 2 mm gesperrt und anschließend mit der Intraoralkamera registriert. Durch die Verwendung der Jigs bleibt in der Gebissaufnahme bereits genügend Platz für die zu konstruierende Schiene, und der Biss muss nicht in der Software nachträglich anhand von Mittelwerten gesperrt werden (Abb. 2 und 3).
Da ich bereits seit über zwölf Jahren Zahnbehelfe am Rechner entwerfe, ging mir der Umgang mit einer 3D-Konstruktionssoftware für Knirscherschienen leicht von der Hand. Doch auch meine Mitarbeiterinnen sollten in der Lage sein, diese Arbeitsschritte zu übernehmen. Würde dies gelingen?
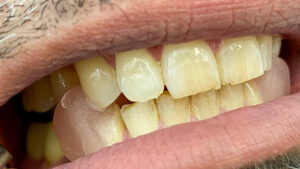
Abb. 2 -Sperrung Biss für die Registrierung
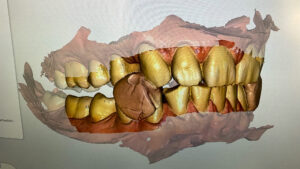
Abb. 3 – Scan-Darstellung der Biss-Sperrung
Umstellung auf den digitalen Workflow
Zu meiner Überraschung stand mein Team den digitalen Anforderungen sehr offen gegenüber. Gerade die jüngeren Team-Mitglieder fühlten sich mit der Software-Anwendung spontan sehr wohl und hatten als Digital Natives keine Berührungsängste. Zwei bis drei Fälle konstruierten wir noch gemeinsam am Rechner, danach konnten die Fachassistentinnen die digitalen Entwürfe bereits selbstständig bearbeiten. Heute werde ich nur noch bei schwierigen Fällen in der Konstruktionsphase dazu gerufen. Ansonsten erfolgt erst am Ende der Modell-Erstellung meine Abnahme oder es wird korrigiert.
Zu Hilfe kam mir bei diesem Delegationsprozess natürlich auch die richtige Software. Als langjähriger Cerec/inLab-Anwender griff ich zunächst zur inLab 20 Software. Ich wollte eine möglichst einfache Anwendung, die es mir mit nur wenigen Mausklicks ermöglicht, eine individuell und optimal erstellte Aufbiss-Schiene zu entwerfen. Noch benutzerfreundlicher gestaltet sich für mich der Workflow allerdings mit der Software DentaMile connect von DMG (Abb. 4).
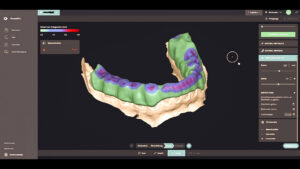
Abb. 4 – Design der Schiene in der DentaMile connect
Diese cloudbasierte Software läuft im Webbrowser und erlaubt mir so auch einen Zugriff von zuhause. Die Software ist intuitiv in der Handhabung, sodass die Mitarbeiterinnen ohne große Einarbeitung in der Software arbeiten können. Ich kann auch vom Homeoffice aus die von meinen Mitarbeiterinnen konstruierten Schienen überprüfen, ggfs. korrigieren und für den Druck freigeben. Denn auch der Drucker selbst ist über die Cloud mit der Konstruktions-Software verbunden und kann von überall in Betrieb genommen werden.
Der materielle Herstellungsprozess, der schon immer im Verantwortungsbereich meiner Mitarbeiterinnen lag, hat sich durch die neue Technik des 3D-Drucks radikal vereinfacht. Während das bisherige Tiefziehen über einem Gipsmodell viele kleinteilige, sich wiederholende und auf präzise Handarbeit ausgerichtete Schritte umfasste, ist der digitale Druckprozess nunmehr ein voll automatisierter, einfach zu bedienender, sauberer Ablauf.
Dazu wird lediglich die Materialwanne mit einem der Indikation entsprechenden Druckmaterial befüllt, wobei dieses über RFID direkt vom Drucker erkannt wird. Nach einem kurzen Wechsel des gedruckten Werkstücks in die Reinigungseinheit 3Dewash wird es dort mit Isopropanol gewaschen und anschließend in der Nachbelichtungseinheit 3Decure nachgehärtet (Abb. 5 und 6).
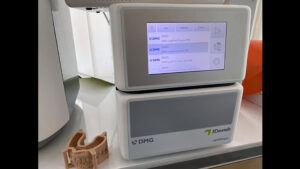
Abb. 5 – Reinigungseinheit 3Dewash
Jeder dieser Schritte läuft voll automatisiert und programmgesteuert. Die Schiene muss lediglich von einer Einheit zur nächsten wechseln und im Anschluss wird sie von der Fachassistenz mit dem Handstück ausgearbeitet und poliert.
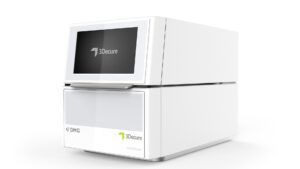
Abb. 6 – Nachbelichtungseinheit 3Decure
Der gesamte digitale Workflow dauert rund 15 Minuten, davon entfallen circa acht Minuten auf den Konstruktionsprozess. Im Vergleich zu dem früheren analogen Herstellungsablauf, der mehr als 1,5 Stunden gedauert hat, ist allein die Zeitersparnis enorm.
Was sagen die Mitarbeiterinnen?
Tatsächlich hat unser neues Verfahren, Aufbissbehelfe digital herzustellen, vieles in unserer Praxis vereinfacht. Ich hatte sicherlich den Vorteil, dass ich selbst sehr technikaffin bin und daher auch meine Mitarbeiterinnen für neue digitale Anwendungen schnell begeistern konnte. Dennoch: Dass die neue Technik nicht nur schneller ist, sondern in ihren Abläufen sogar Spaß macht, hat uns alle positiv überrascht.
Die Konstruktion der Schienen am Rechner ist für meine Mitarbeiterinnen bequemer und sauberer als die Arbeit mit Gipsmodellen. Außerdem können sie bei einem Gestaltungsfehler in der Software einfach einen Mausklick zurückspringen und müssen nicht gleich ganz von vorne anfangen. Diese Freiheit, quasi nichts kaputt machen und auch einiges ausprobieren zu können, fühlt sich tatsächlich sehr erleichternd an.
Und auch die Arbeit mit dem 3D-Drucker selbst funktioniert so einfach und fehlerresistent, dass auch die Mitarbeiterinnen aus der Verwaltung Freude an der Herstellung und Ausarbeitung der gedruckten Schienen haben. Besonders geschätzt wird der sehr viel saubere Arbeitsablauf im Vergleich zum manuellen Tiefziehen der Schienen. Dass der gesamte digitale Produktionsprozess deutlich weniger Zeit beansprucht und meinen Mitarbeiterinnen dadurch mehr Raum für andere wichtige Aufgaben im Praxisalltag bleibt, ist sicherlich ebenso erfreulich.
Abschließend stelle ich fest – und das ist vielleicht der wichtigste Punkt überhaupt: Dadurch, dass fast der komplette Herstellungsprozess der Schienen in der Hand meiner Mitarbeiterinnen liegt, sie das Produkt wirklich vom Anfang bis zum Ende begleiten, fühlen sie sich am Ende des Tages deutlich zufriedener mit ihrer Arbeit.
Ich bin froh, dass ich den Tätigkeitsbereich meines Teams ausweiten konnte. Und sie sind mittlerweile jedes Mal ein wenig stolz, wenn eine ihrer Schienen beim Patienten eingegliedert wird (Abb. 7).
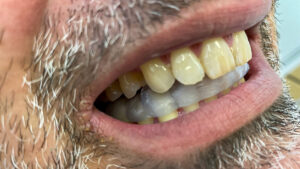
Abb. 7 – Fertiges Aufbissbehelf im Patientenmund
Kontakt
Dr. Alexander Schnellert
ist in eigener Praxis in Hamburg Eppendorf niedergelassen. Sein Tätigkeitsschwerpunkt ist die Parodontologie. Zu seinem weiteren Behandlungsspektrum gehören Implantologie, Kinderzahnheilkunde, Prophylaxe, Vollkeramikrestaurationen, Endodontie, Zahnersatz und Ästhetische Zahnmedizin.