Wie sich ein Werkstoff zum Gamechanger entwickelte
Vor 15 Jahren startete Amann Girrbach als eines der ersten Unternehmen mit der Herstellung und dem Vertrieb von Zirkonoxid-Rohlingen zur Produktion von Zahnersatz. Fünf Jahre später folgte die Einführung der Marke Zolid: Anwendern standen erstmals CAD/CAM-Rohlinge zur Verfügung, die ohne aufwendige Verblendungsprozesse eine hohe Ästhetik erzielten.
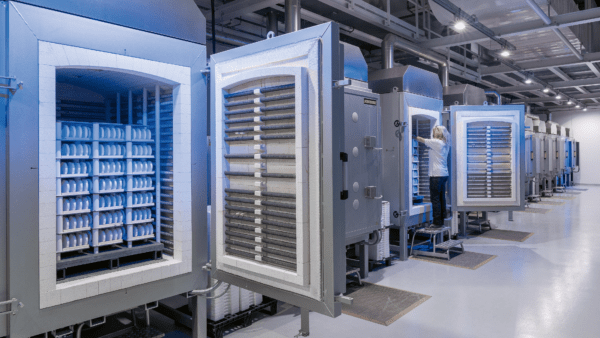
01 – Zirkonoxid-Rohlinge werden zu 100 % in Österreich produziert.
Seither hat das Unternehmen Materialien und Verarbeitungsprozesse kontinuierlich weiterentwickelt und eine große Zahl treuer Kunden gewonnen. Im Gespräch diskutieren Falko Noack, Vice President Research & Development bei Amann Girrbach, Prof. Dr. Dipl.-Ing. (FH) Bogna Stawarczyk, M.Sc., Wissenschaftliche Leiterin Werkstoffkunde der Poliklinik für Zahnärztliche Prothetik an der Ludwig-Maximilians-Universität München und die beiden Zahntechnikermeister Benjamin Votteler, Votteler Dentaltechnik GmbH & Co. KG in Pfullingen, und Rosa Winterhalter, Lindauer Zahntechnik GmbH in Lindau, über die Vorteile des Materials Zirkonoxid, die Erfahrungen und Weiterentwicklungen der vergangenen Jahre sowie mögliche Herausforderungen der Zukunft.
Herr Noack, Sie haben sich bereits während Ihres Studiums mit dem Material Zirkonoxid und dessen Anwendungen beschäftigt – und intensiver dann in den vergangenen 15 Jahren im Rahmen ihrer Tätigkeit bei Amann Girrbach. Wie waren die Anfänge und was hat sich getan in all diesen Jahren?
NOACK: Zirkonoxid erschien mir schon während meines Studiums als eine ideale Alternative zu den damals bestehenden Werkstoffen. Allerdings waren die gesicherte Verarbeitung und die begrenzte Einsetzbarkeit stark limitierende Faktoren. Als ich nach meinem Studium die Gelegenheit bekam, mich bei Amann Girrbach damit auseinanderzusetzen, war ich sofort begeistert. Der Aufbau der Zirkonoxid-Rohlingsproduktion und die anwendungsseitige Betreuung erster gesicherter Bearbeitungsmethoden, wie dem Kopierfräsen, waren sehr spannende Projekte – wir konnten damit immens wichtiges Grundlagenwissen generieren (Abb. 1). Seit seiner Einführung ging Zirkonoxid quasi durch die Decke. Kaum ein anderes Material hat eine solche Weiterentwicklung erfahren. Alle verarbeitungsseitigen Fragestellungen, von der mittlerweile nahezu ausschließlichen CAM-seitigen Bearbeitung über das richtige Sintermanagement bis hin zur Verblendung, sind mittlerweile als gesichert gelöst einzustufen. Zirkonoxid hat auch im ästhetischen Bereich eine steile Performance-Kurve hinter sich und ist damit, dank gesteigerter Transluzenz und verbesserten Farbeigenschaften, auch monolithisch einsetzbar. Die klinischen Langzeitergebnisse belegen eine sehr gute Eignung und eine hervorragende Überlebensrate für vielfältigste festsitzende Indikationen. Produktionsseitig hat sich enorm viel getan: Die Produktionsfläche für unsere Rohlinge hat sich gegenüber dem initialen Setup verzwanzigfacht und wurde fortlaufend mit modernster Technologie ausgebaut. Wir sind mittlerweile einer der fünf weltweiten, größten Produzenten für dentale Zirkonoxid-Rohlinge.
Welche waren konkret die wichtigsten Innovationen in diesem Zusammenhang?
NOACK: Sicherlich Ceramill ZI, unser erster eigenentwickelter Zirkonoxid-Rohling. Mit diesem Material ist es uns gelungen, die Herstellung von maximal weitspannigen Restaurationen gesichert anbieten zu können – das war eine Basisinnovation. Wesentlich ist auch die Entwicklung von Ceramill Zolid: Wir waren damals auf der Suche nach besserer Ästhetik und höherer Transluzenz. Einige Hersteller gingen hierfür den Weg, die Sintertemperaturen zu erhöhen – was, wie man heute weiß, zwar der einfachere Weg war, jedoch aus werkstoffkundlicher Sicht auch der risikoreichere. Zusammen mit unserem langjährigen Entwicklungspartner und exklusiven Rohmateriallieferanten Tosoh Corp. Japan ist es in intensiver Zusammenarbeit gelungen, unser erstes transluzentes Material zu entwickeln, das ohne Erhöhung der Sintertemperaturen auskommt. Wichtige Innovationen waren zudem die ästhetischen Zirkonoxid-Materialien Zolid FX Multilayer und Zolid Gen-X Multilayer, die durch ihre Transluzenz und Farbverläufe vielseitig monolithisch für festsitzenden Zahnersatz Anwendung finden (Abb. 2 bis 4). Die letzte große Innovation der jüngeren Vergangenheit stellt sicherlich Zolid DRS dar, ein Material, das mit Hilfe des dazugehörigen Sinterofens Therm DRS in 20 Minuten gesintert werden kann. Allein die Verkürzung der Sinterzeit von ehemals acht Stunden auf weniger als ein Sechzehntel zeigt, welche Fortschritte durch permanente Weiterentwicklung erzielt werden konnten.
Frau Prof. Stawarczyk, im Rahmen Ihrer Tätigkeit als wissenschaftliche Leiterin für Werkstoffkunde an der Universität München, wurden Sie bereits mehrfach mit der Begutachtung von Materialien von Amann Girrbach betraut. Erinnern Sie sich an die Anfänge Ihrer Expertisen zu Zirkonoxid und an anschließende Entwicklungen?
STAWARCZYK: Ja, ich erinnere mich gut daran: Ich habe bereits sehr früh die ersten Zirkonoxid-Ronden für Amann Girrbach begutachtet – und weiß wieviel Wissen und Arbeit dahinterstecken. Umso mehr freut es mich, wie erfolgreich Zirkonoxid geworden ist und wo Amann Girrbach heute steht. Wir haben beinahe jede Zirkonoxid-Modifikation von Amann Girrbach bei uns untersucht und kennen die Materialien bestens. Unser aktuellstes gemeinsames Projekt war die Entwicklung eines High-Speed-Sinterofens mit passendem Zirkonoxid – der seit vergangenem Jahr auch schon auf dem Markt ist. Diese Entwicklung wurde im Rahmen eines ZIM-Kooperationsprojekts, also im Rahmen des Förderprogramms „Zentrales Innovationsprogramm Mittelstand“, durchgeführt – aufbauend auf dem Vorwissen, das wir gemeinsam über zahlreiche Jahre gesammelt haben.
Wie bewerten Sie die Zukunft von Zirkonoxid in der dentalen Anwendung – und wo liegen die Schwerpunkte der Forschung?
STAWARCZYK: Zirkonoxid ist seit der Einführung erst als 3Y-TZP-Werkstoff, seit 2015 als 5Y-TZP- und seit 2017 mit der 4-TZP-Modifikation auf dem dentalen Markt. Seit Jahren arbeitet man also an der Ver- und Bearbeitung dieses Materials. Es ist gelungen, mit weiterhin guten mechanischen Eigenschaften diesen Werkstoff schneller zu sintern, sodass wertvolle Arbeitszeit eingespart werden kann. Durch die verschiedenen Modifikationen wurde der Werkstoff zudem immer ästhetischer. Die Einfärbrezepturen werden laufend optimiert – und die Ästhetik stets mit jener der Silikatkeramiken verglichen. Die verschiedenen Modifikationen werden zunehmend innerhalb eines Rohlings kombiniert, um eine gute Ästhetik und hohe mechanische Eigenschaften zu erzielen. Im Moment liegt, meiner Meinung nach, der Schwerpunkt in der Betrachtung des Gesamtsystems, dazu zählen auch die CAD/CAM-Verarbeitung und die Positionierung der Ronden in der Software. Es wird insgesamt versucht, immer mehr zu automatisieren und „künstliche Intelligenz“ auch in diesem Bereich einzusetzen.
Herr Votteler, Frau Winterhalter – aus Sicht der Anwender, inwieweit haben sich Arbeitsweisen und Methodik mit der Verwendung von Zirkonoxid in den letzten Jahren verändert?
VOTTELER: Die größte Veränderung in der Arbeitsweise ist generell der Umstieg von analog zu digital: Digitales Arbeiten ist wesentlich effizienter, genauer, reproduzierbarer. Früher wurde viel Zeit für das Modellieren und das manuelle Kopierfräsen verwendet. Heute wird direkt auf Intraoralscans weitergearbeitet und die Zeit somit am Rechner verbracht. Bei den Materialien selbst ist es so, dass ich opakes, weißes Zirkonoxid nur noch für Primärteleskope nutze, für mache Implantat-Abutments – diese brauchen immer eine Verblendung aus Schichtkeramik um die Ästhetik natürlicher Zähne zu erreichen. Die Festigkeit von Schichtkeramik liegt bei ca. 90 bis 100 MPa, die Festigkeit von Transparenten Multilayer-Zirkon liegt bei ca. 1000 MPa, also dem ca. 10-Fachen. Das bedeutet, ich habe eine viel stabilere Basis und brauche im Schneidezahn-Gebiet nicht mit Schichtmasse zu verblenden. Im Frontzahngebot reicht eine dünne labiale Verblendung. Und mit der Einführung von Zolid HT+ habe ich auch die Vollverblendung aufgegeben: Monolithisch ist stabiler, effizienter in der Herstellung und mittlerweile auch sehr ästhetisch.
WINTERHALTER: Wir haben bei uns im Labor schon von Anfang an digital und analog gearbeitet. Bei den Materialien kommt bei uns je nach Fall entweder opaques Zirkon oder Zolid Gen-X zum Einsatz. Für einen schnellen Ablauf im Labor wird Vollzirkon verwendet und wenn es um individuelle Arbeiten geht, nehmen wir Zirkon verblendet.
Warum entscheiden Sie sich seit vielen Jahren für Materialien von Amann Girrbach – trotz wachsender Konkurrenz?
VOTTELER: Für mich macht das gesamte Konzept von Amann Girrbach einfach Sinn: Eine Sintertemperatur für alle Zirkone, hochästhetische SHT-Zirkone (FX ML) für hochästhetische Fälle und Gen-X für alles andere – mehr brauche ich nicht. Auf Einschränkungen der Festigkeit habe ich offen gesprochen einfach keine Lust – das ist eine klare Fehlerquelle, vor allem, was den Brückenverbinder angeht. Stabilität steht für mich an erster Stelle. Da ich nun über ein solch ästhetisches Zirkon wie Gen-X verfüge, benötige ich nichts Anderes mehr. Da nur Tosoh-Rohmaterial zum Einsatz kommt, kostet zwar der Blank ein wenig mehr als anderes Zirkon, welches nur teilweise Tosoh-Pulver oder gar kein Tosoh-Pulver beinhaltet, aber das ist es auf alle Fälle wert. Denn Amann Girrbach-Zirkone altern nicht – und das ist mir was Langzeiterfolge angeht sehr wichtig
WINTERHALTER (Schmunzelt): Ich erzähle immer den anderen Firmen, dass wir mit Amann Girrbach verheiratet sind. Da wir Sternlabor und Key Opinion Leader sind, wollen wir auch keine anderen Materialien im Labor verwenden – Qualität ist uns einfach zu wichtig und wir möchten keine Experimente eingehen oder zweitbeste Lösungen erhalten.
Was erwarten Sie in Zukunft von der Industrie in Bezug auf Zirkonoxid und dessen Verarbeitung?
VOTTELER: Was ich mir noch erwarte oder auch wünschen würde, wäre einzig ein Multilayer-Zirkon mit noch etwas transparenterem Schneideanteil, aber voller Festigkeit.
Winterhalter: Eigentlich bin ich sehr zufrieden mit den Materialien und benötige diesbezüglich aktuell nichts mehr. Was ich mir allerdings wünsche ist, dass die Industrie mehr Indikationen freigibt.
Abschließend, Herr Noack, worin sehen Sie aus Herstellersicht aktuell die größten Herausforderungen im Zusammenhang mit Zirkonoxid?
NOACK: Meiner Meinung nach sind aus technischer Sicht die anwendungsseitigen Fragestellungen als gelöst zu betrachten. Die Herausforderung ist aktuell, den Überblick bei der Vielzahl von Produkten zu behalten. Grundsätzlich sehe ich hier aber Licht am Ende des Tunnels, da sich mehr und mehr die Zirkonoxid-Generationen herauskristallisieren, die multifunktional einsetzbar sind und damit in Zukunft vorherrschend sein werden. Aus Herstellerperspektive sind die Herausforderungen sicher die ständig steigenden, gesetzlichen und damit dokumentarischen Pflichten und Vorgaben, die es zu bewältigen gilt. Diese Vorgaben empfinden wir allerdings als sehr positiv, da sie zu mehr Sicherheit des Medizinproduktes und damit auch für die Patienten ‧beitragen.