Reise durch die Welt der Zirkonoxide
#Algorithmen, #Digitalisierung, #Künstliche Intelligenz, #Transformation – bei diesen Schlagworten weiß jeder: Hier geht es um die Zukunft! Und im Gegensatz dazu: die Werkstoffkunde. Ein Begriff, der für viele zunächst vielleicht wenig attraktiv wirkt. Doch zu Unrecht! Denn auch in der Zahnmedizin bilden erst die entsprechenden Werkstoffe die Grundlage für Weiterentwicklungen und Zukunftsperspektiven. „Die Zukunft beginnt gestern“: Diese Artikelserie informiert über die Entwicklung dentaler CAD/CAM-Werkstoffe und sensibilisiert für die Relevanz eines fundierten Werkstoffkunde-Wissens. Teil 1 beschäftigt sich mit dem Thema Zirkonoxid.
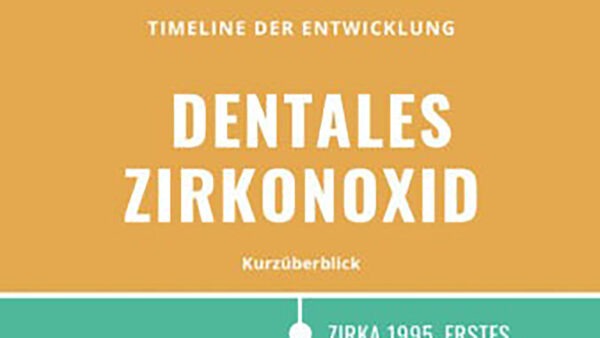
Zirkonoxid sorgt in der Zahnmedizin und Zahntechnik seit einem Vierteljahrhundert für spannende Entwicklungen. Kaum ein anderer Werkstoff revolutionierte die Zahnersatzfertigung so sehr wie dieses Material. Es ist zu vermuten, dass sich ohne die Weiterentwicklung von Zirkonoxiden auch die CAD/CAM-Fertigung nicht im aktuellen Maße etabliert hätte. Allen anfänglichen Unkenrufen zum Trotz hat sich Zirkonoxid zu einem nahezu unverzichtbaren Material entwickelt.
Wie alles begann
Das erste dentale Zirkonoxid wurde vor mehr als 25 Jahren auf den Markt gebracht. Das durchgesinterte Zirkonoxid (gehippt) war so hart, dass das Fräsen mehrere Stunden dauerte und mit einem hohen Werkzeugverschleiß verbunden war. Nicht nur wirtschaftlich, auch aus Sicht der Werkstoffkunde blieben viele Fragen offen. Zwar hatte das Material eine hohe initiale Festigkeit, doch die Folgen der Bearbeitung (gegebenenfalls Phasenumwandlung) auf die Langzeitstabilität waren nicht bekannt. Den nächsten Schritt in der Entwicklung machte Ende der 1990er Jahre die ETH (Eidgenössische Technische Hochschule) Zürich zusammen mit der Firma DeguDent. Das Unternehmen brachte schließlich den ersten Zirkonoxid-Grünling auf den Markt. Dieser war aufgrund der noch enthaltenen Bindemittel deutlich weicher und ließ sich einfacher fräsen. Die Bindemittel (Wachse, Kunststoffe) wurden hier erst nach dem Fräsen beim Sintern komplett ausgebrannt. Da Grünlinge jedoch sehr weich sind, war die Gefahr von Materialschädigungen bei der Bearbeitung hoch. Heute wird Zirkonoxid daher nur noch als Weißling angeboten (Abb. 1). Bei einer industriellen Vorsinterung werden die Bindemittel vollständig verbrannt und das Material für die Bearbeitung stabilisiert. Von nun an etablierte sich Zirkonoxid in der Zahnmedizin beziehungsweise zunächst in der Zahntechnik in Rondenform (Disk) und später als Block für die Chairside-Fertigung (Einzelzahnrestaurationen, kleine Brücken). Hergestellt wird Zirkonoxid in der Regel aus Pulver (Zirkonium), dem nach einer Reinigung und einer chemischen Vorbehandlung verschiedene Zusätze (zum Beispiel Yttrium) zudotiert werden. Die Rohmaterialien stammen von einigen wenigen Lieferanten, die das Pulver an Zirkonoxid-Hersteller liefern (Abb. 2). Zirkonoxid-Rohlinge sind in Rondenform für die Labside-Fertigung und in Blockform für die Lab- und Chairside-Fertigung verfügbar (Abb. 3).
Zirkonoxid wird ästhetisch
Ende der 1990er Jahre
Zirkonoxid hat eine sehr hohe Festigkeit, ist jedoch sehr opak und tetragonal metastabil. Daher wird dieses Material konventionell mit Keramikmassen verblendet.
2. Generation (IDS Jahr 2013)
Basierend auf dem Wunsch nach einer vereinfachten, monolithischen Fertigung entwickelten die Hersteller tetragonal metastabiles Zirkonoxid weiter und modifizierten den Werkstoff. Für die zweite Generation wurden die Korngröße verkleinert, die Anteile von Aluminiumoxid reduziert und auf die Korngrenzen von Zirkonoxid positioniert. Dadurch konnte ‧eine etwas höhere Transluzenz erzielt werden. Gleichwohl sind die mechanischen Eigenschaften nahezu gleich hoch ‧geblieben.
In dieser Zeit wurde auch das erste Multilayer-Zirkonoxid entwickelt (Kuraray Noritake). Heute bieten viele Anbieter mehrschichtige Rohlinge an. Es werden Rohlinge mit drei bis sieben verschiedenen Schichten angeboten. Durch den Farbverlauf innerhalb des Rohlings kann auf vereinfachtem Weg eine höhere Ästhetik erzielt werden.
3. Generation (IDS Jahr 2015)
Um die Lichtoptik von Zirkonoxid noch mehr den ästhetischen Silikatkeramiken anzunähern, ging die Entwicklung weiter. 2015 kam die 3. Generation der Zirkonoxide auf den Markt (Abb. 4). Es wurde auf die kubische Phase gesetzt, welche größere Kristalle aufweist und damit auch das Material transluzenter erscheinen lässt. Dieses Material befindet sich zu circa 50 Prozent in der kubischen und 50 Prozent in der tetragonalen Phase. Herstellerabhängig werden hohe Transluzenzwerte nah an denen von Silikatkeramik erreicht. Zusätzlich zur Transluzenz wurden weitere Parameter optimiert, zum Beispiel Fluoreszenz und Opaleszenz. Allerdings sind die mechanischen Eigenschaften bei der 3. Generation deutlich reduziert.
4. Generation (IDS Jahr 2017)
Die 4. Generation von Zirkonoxid kam 2017 auf den Markt. Dieses Material befindet sich zu circa 30 Prozent in der kubischen und 70 Prozent in der tetragonalen Phase. Die mechanischen Eigenschaften sind wieder etwas erhöht worden. Zudem ist die Transluzenz vergleichsweise hoch, jedoch etwas geringer als bei der 3. Zirkonoxid-Generation (Abb. 5).
Multi-Generationen-Zirkonoxid (IDS Jahr 2019)
In weiteren Entwicklungsprozessen gelang es, in einem Rohling verschiedene Zirkonoxid-Generationen zu vereinen. Ergebnis ist eine hohe Festigkeit im Kern des Materials (zum Beispiel Verbinderbereiche, 3Y-TZP) und eine hohe Transluzenz im Inzisalbereich (4Y-TZP beziehungsweise 5Y-TZP). Die Farbe wird durch die Rezepturen der Farbgradienten im Pulver (gelb, pink, grau, weiß) und die Transluzenzen durch das Verwenden verschiedener Generationen von Zirkonoxid erzielt. Außerdem gilt stets die Regel: Je heller das Material eingefärbt ist, desto transluzenter ist es.
Optimierte Verarbeitung
Die Weiterentwicklung von Zirkonoxid betrifft zudem die vereinfachte Anwendung. Der konventionelle Sinterprozess dauert mehr als neun Stunden. Ein Verändern der Sinterparameter (Aufheizrate, Haltezeit, Haltetemperatur, Abkühlrate) beeinflusst hierbei die mechanischen und optischen Eigenschaften. Der Wunsch nach einem effizienten Vorgehen führte dazu, dass das schnelle Sintern – gerade bei den transluzenteren Zirkonoxiden – immer interessanter wird. Seit 2017 ist das Speed-Sintern mit einer Gesamtsinterzeit von 120 Minuten möglich. Seit 2019 gibt es High-Speed-Sinteröfen für das Sintern von kleineren Restaurationen (bis zu drei Einheiten) innerhalb von bis zu 30 Minuten. High-Speed-Sintern ist nur mit speziellen Sinteröfen (Dentsply Sirona, Amann Girrbach) für dafür freigegebene Zirkonoxide empfohlen (Abb. 6).
Heute und morgen
Basierend auf den Entwicklungen während der vergangenen 25 Jahre gilt Zirkonoxid in vielen Anwendungen als Material der Wahl. Populär werden immer mehr monolithische Restaurationen, die in vielen Fällen zu einer guten Ästhetik bei zugleich hohen mechanischen Eigenschaften und einer effizienten Fertigung führen. Es wird immer mehr auf standardisierte Prozesse und eine möglichst effiziente Anwendung Wert gelegt. Ziel ist es, mit hoher Zuverlässigkeit und in einer volldigitalen Prozesskette zum Ergebnis zu gelangen. Zudem stehen für die ästhetische Individualisierung spezielle keramisch-basierte Malfarben bereit, die dem monolithischen Zirkonoxidgerüst noch mehr Lebendigkeit verleihen – entweder als Mikroschichtung nach einem Cut-back oder als Malfarbe zur Oberflächen-Charakterisierung. Auch ist es bereits möglich, Zirkonoxid im 3D-Druck zu bearbeiten. Hier zählt die österreichische Firma Lithoz zu den Vorreitern. Allerdings muss diese Technologie noch in weiteren In-vitro- und In-vivo-Untersuchungen geprüft werden.
Die Zukunft beginnt gestern
Die kurze Darstellung der Entwicklung von Zirkonoxid zeigt, wie stark Werkstoffkunde das Etablieren der CAD/CAM-gestützten Fertigung und somit die Zukunft der digitalen Zahntechnik beeinflusst. Zahnmediziner und Zahntechniker sollten Einblick in die Werkstoffkunde haben und unter anderem die Unterschiede zwischen den Zirkonoxiden einordnen können. Für einen einfachen Zugang zur Werkstoffkunde kann das digitale Werkstoffkunde-Kompendium (www.werkstoffkunde-kompendium.de) genutzt werden. Das fundierte Grundlagenwissen rund um moderne dentale Materialien ist grafisch ansprechend aufbereitet und wird ergänzt durch wertvolle Tipps sowie Produkthinweise.
Diese Serie geht weiter in der nächsten Ausgabe mit Teil 2, der die Entwicklung der dentalen Keramiken, speziell der verstärkten Silikatkeramiken, behandeln wird.